Advantages of Lost Wax Investment Casting
High Precision and Detail
Lost Wax Casting can achieve extremely tight tolerances (often within ±0.1 mm or better) and intricate features that are difficult or impossible to achieve with other casting methods.
Excellent Surface Finish
The ceramic shell provides a smooth surface that often requires minimal post-processing. Parts can be produced with very fine details, making it an ideal method for industries that require high-quality finishes, such as jewelry and medical devices.
Material Versatility
Lost Wax Casting can accommodate a wide range of materials, including various metals (stainless steel, titanium, gold, brass, etc.), making it suitable for different industries.
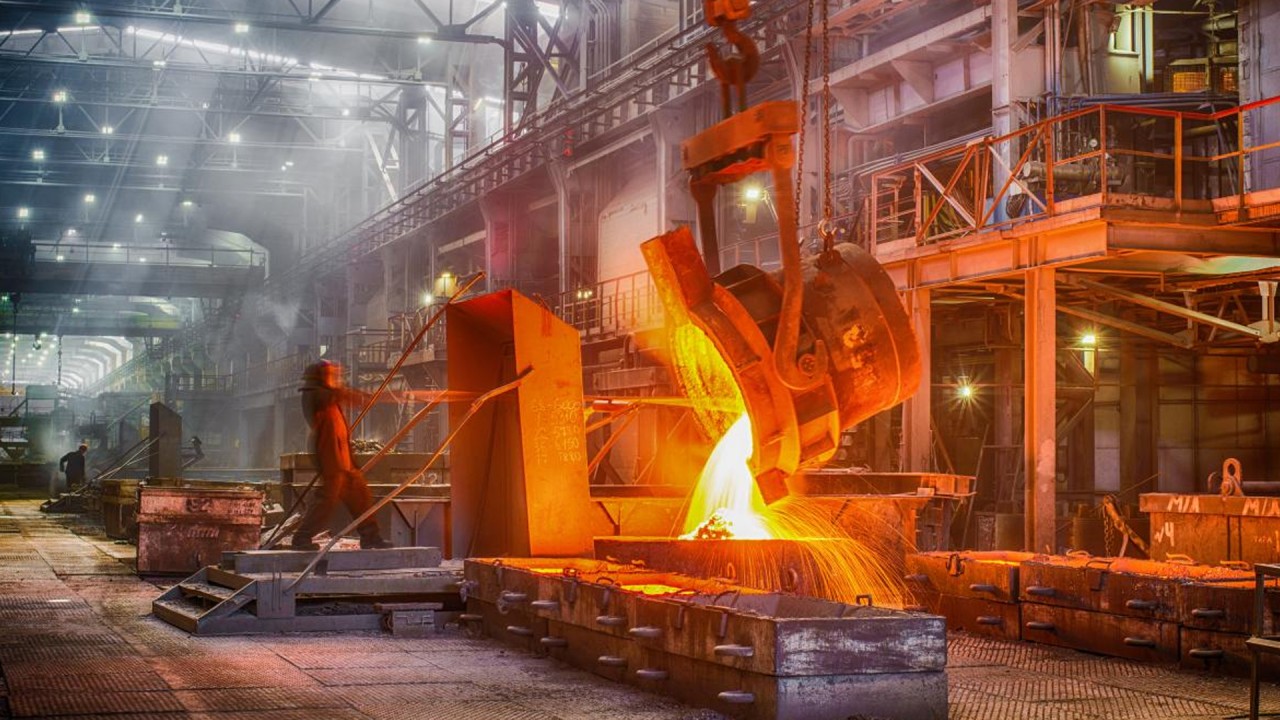
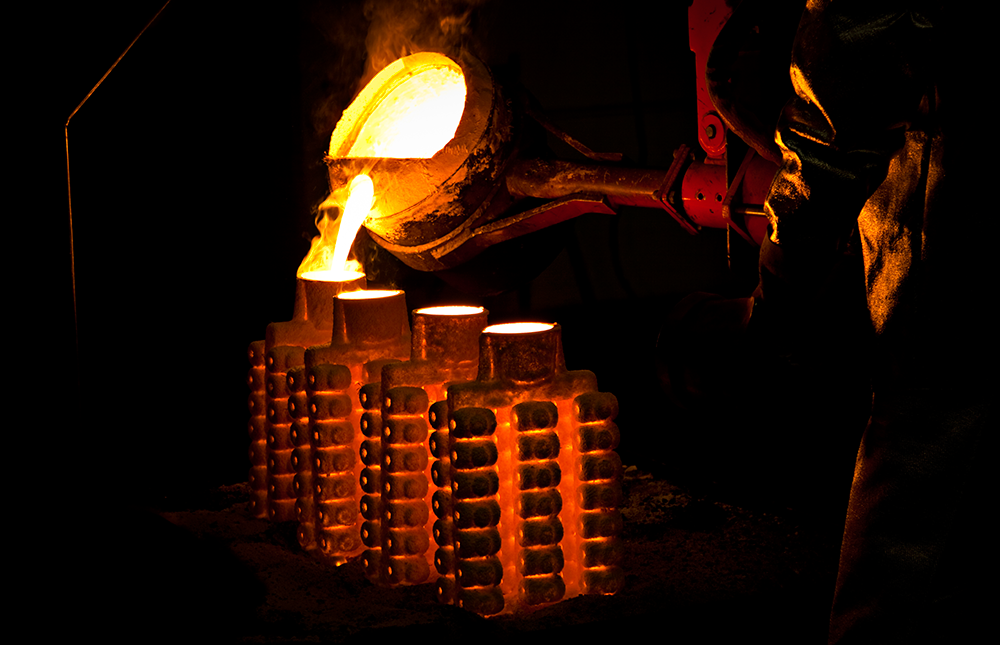
Lost Wax Investment Casting Metals
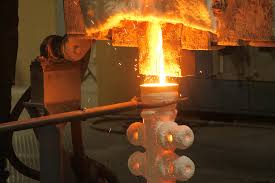
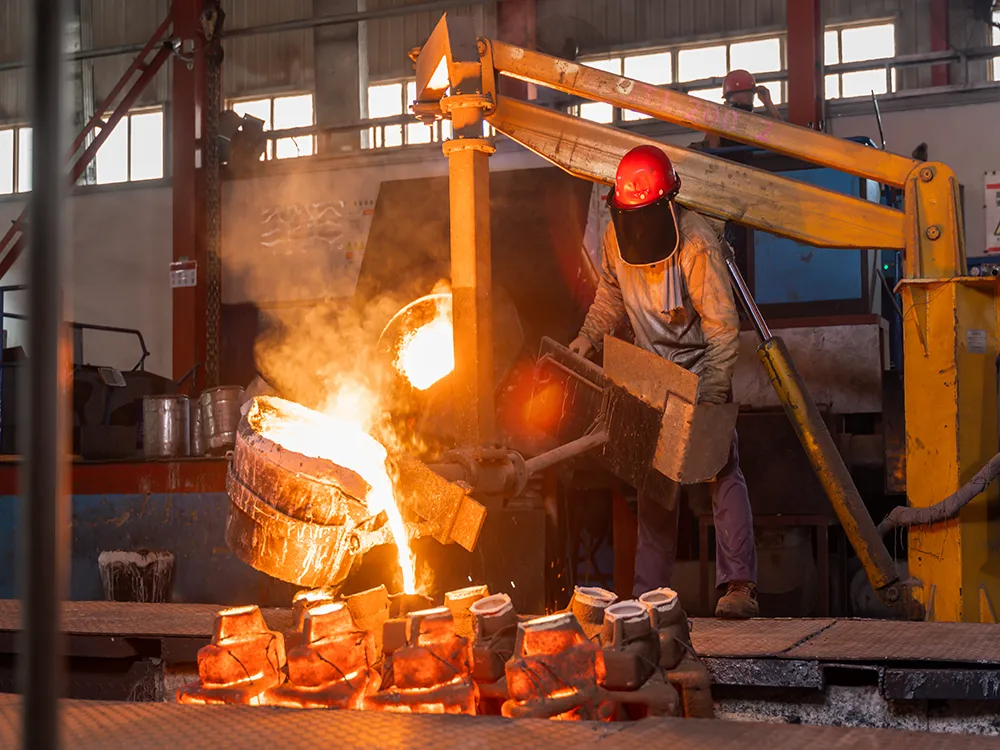
Carbon Steel: from Low Carbon Steel to High Carbon Steel, AISI 1020 – AISI 1060,
Alloy Steel: ZG20SiMn, ZG30SiMn, ZG30CrMo, ZG35CrMo, ZG35SiMn, ZG35CrMnSi, ZG40Mn, ZG40Cr, ZG42Cr, ZG42CrMo…etc on request.
Stainless Steel: AISI 304, AISI 304L, AISI 316, AISI 316L, CF8M, CF8, 1.4408…etc. Precipitation Hardening Stainless Steel and other stainless steel grade.
Duplex Stainless Steel: 1.4460, 1.4462, 1.4468, 1.4469, 1.4517, 1.4770, 2205, 2507.
Nickel Base Alloys: Hastelloy-C, Inconel 625 etc.
Cobalt Base Alloys.
Brass, Bronze & Copper based alloys.
Applications of Precision Investment Castings
Components made by investment casting are utilized to cast a wide variety of items, including high quality, high performance industrial parts of complex structures.
The application of the precision investment casting (lost wax casting process) components covers a wide range of industries, in our foundry they are typically used in the following areas (including but not limited to):
- Rail Trains
- Heavy Duty Trucks
- Automotive
- Construction Equipment
- Logistics Equipment
- Agricultural Equipment
- Hydraulics
- Engine Systems
Applications of Precision Investment Castings
Capabilities of Lost Wax Investment Casting
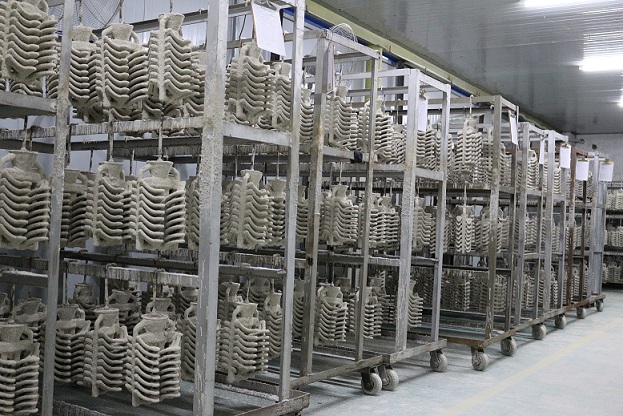
-
Max Size per Casting: 1,000 mm × 800 mm × 500 mm
-
Weight Range: 0.01 kg – 100 kg
-
Annual Capacity: 2,000 tons
-
Binder Materials: Silica Solution (Silica Sol), Water Glass (Sodium Silicate) or their mixtures
-
Casting Tolerances: CT4~CT8 or on request according to ISO & IATF .
VARTIS ENGINEERING PVT LTD. is a leading precision casting foundry in China of top-quality investment castings committed to delivering excellent quality, superior value and exceptional customer experience. VARTIS ENGINEERING PVT LTD. has the experience, technical expertise and quality assurance processes to consistently and reliably deliver an extensive range of precision castings with further processing.
Steps of Lost Wax Investment Casting Process
Investment casting is a multi-step process that produces near-net shape precision casting parts. The process begins with wax being injected into a die to create a replica pattern of the finished product. The patterns are then affixed to wax runner bars to create the cluster. A special machine dips the cluster repeatedly into a slurry to develop a ceramic shell, and then the wax is removed in a steam autoclave. Once the wax is removed, the ceramic shell is preheated and then filled with molten metal to create the desired castings.
Investment casting requires a metal die (usually in aluminum), wax, ceramic slurry, furnace, molten metal, and other machines needed for wax injection, sand blasting, vibratory tumbling, cutting, and grinding. The lost wax investment precision casting process mainly involves the following steps:
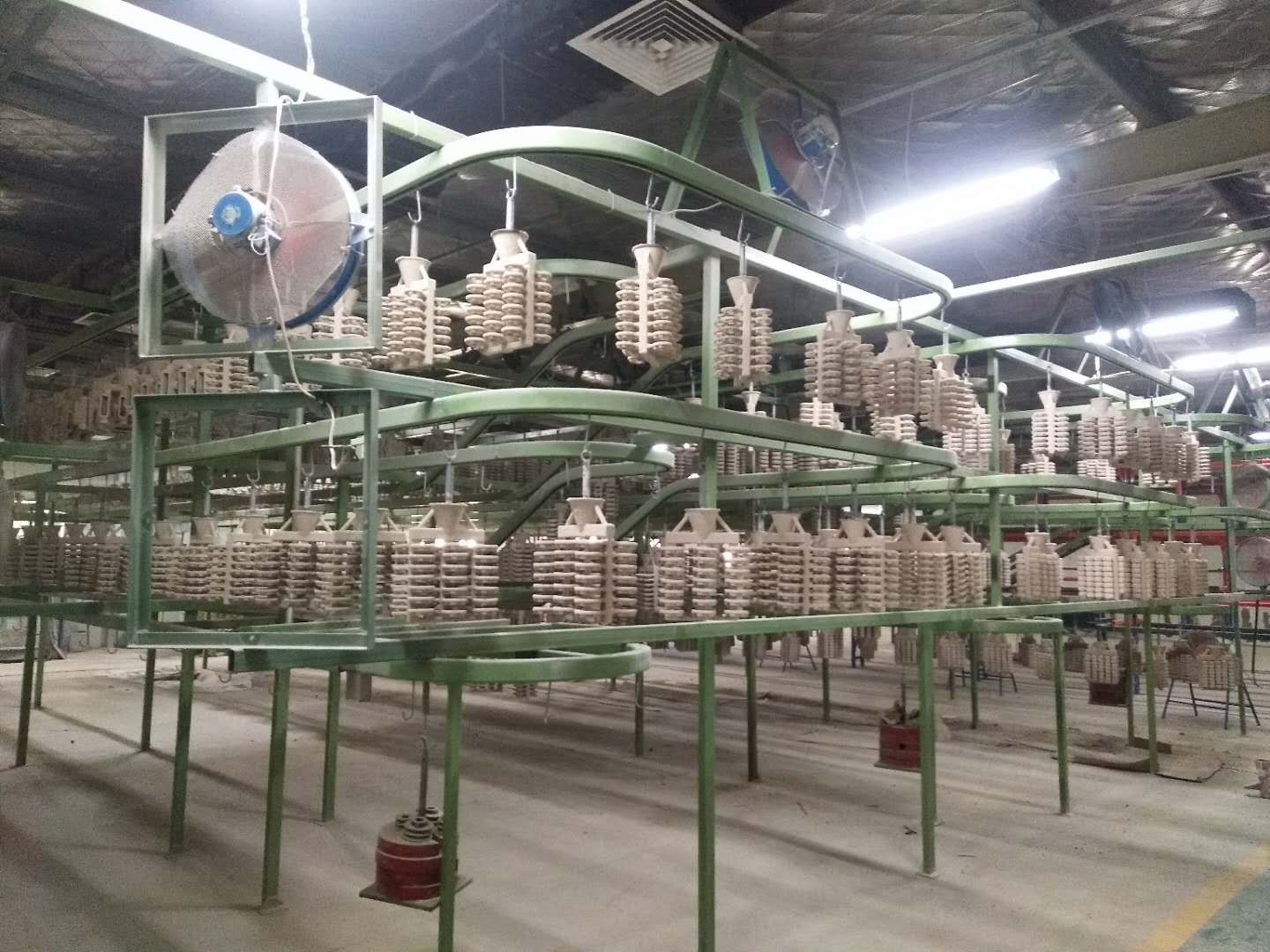
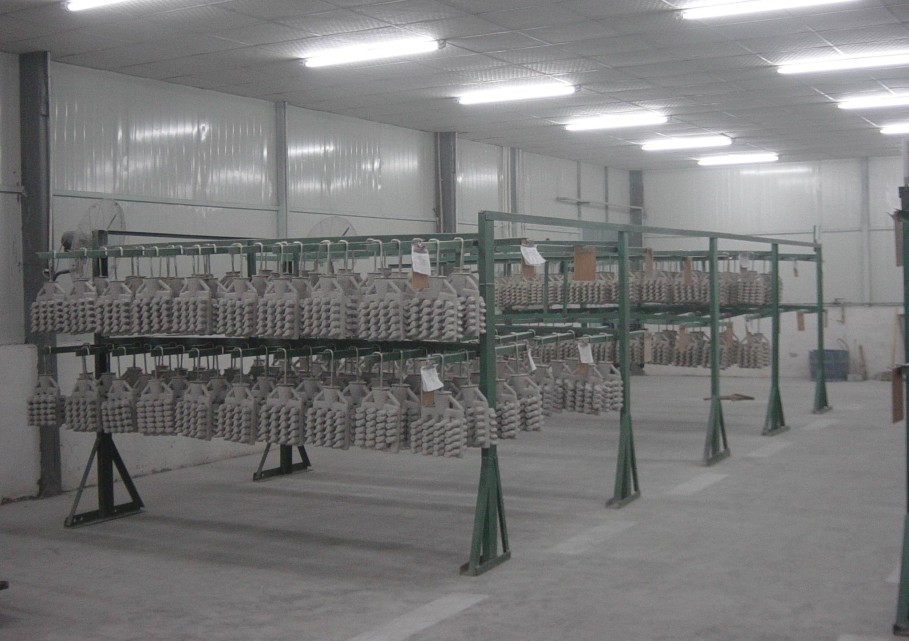
1- Metal Die Making
Based on the drawings and requirements of the desired casting parts, the metal die or mold, usually in aluminum, will be designed and produced. The cavity will form the same size and structure of desired castings, under the premise of considering the machining allowance.
2- Wax Injection
Also as known as pattern formation, lost wax casting patterns are created by injecting molten wax into the metal die produced in last process. The special wax injextion machines should be used for this process
3- Slurry Assembly
After fixing (if needed), the wax patterns are then attached to a gating system, which usually is a set of channels through which a molten metal flows to the mold cavity. After that, a structure like a tree is formed, which is suitable for mass casting at the foundry.
4- Shell Building
The investment castings outer shell casing is built up through dipping into a ceramic bath and then immediately coated with sand for several times. The process is usually repeated for many times and last for days in order to make sure the shell strong enough to withstand the molten metal later on.
5- De-waxing
The inner cavity of precision investment casting is then dewaxed, which leaves a hollow outer ceramic shell layer. The hollows are just the same space as the desired castings. During this process, the wax could be collected for re-usage.
6- Pouring & Solidification
Before pouring, the ceramic shell with cavity should be pre-heated. This prevents shock and the ceramic shell from cracking once the liquid metal at a high temperature is poured into the cavity. The chemical composition of the molten metals should also be tested before casting.
7- Sawing or Cutting
Once the molten metal has been cooled and solidified, the cast part(s) is then removed from the gating system tree cluster via shaking, cutting or friction sawing off the individual raw casting.
8- Shot Blasting and Secondary Processing
The casting part is then fully customized through grinding or additional heat treatments. Secondary machining or surface treatment might also be required depending on the requirements of the part.
9- Packing and Delivery
Then the lost wax casting parts will be fully tested for the dimensions, surface, mechanical properties and other required tests before packing and delivery.
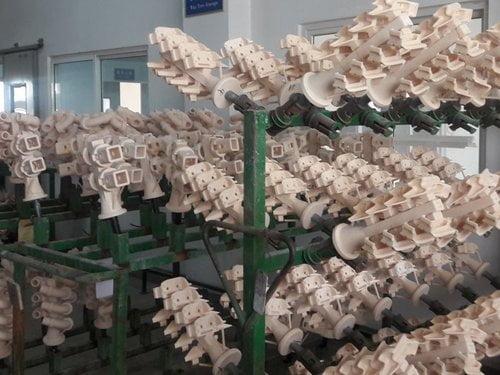
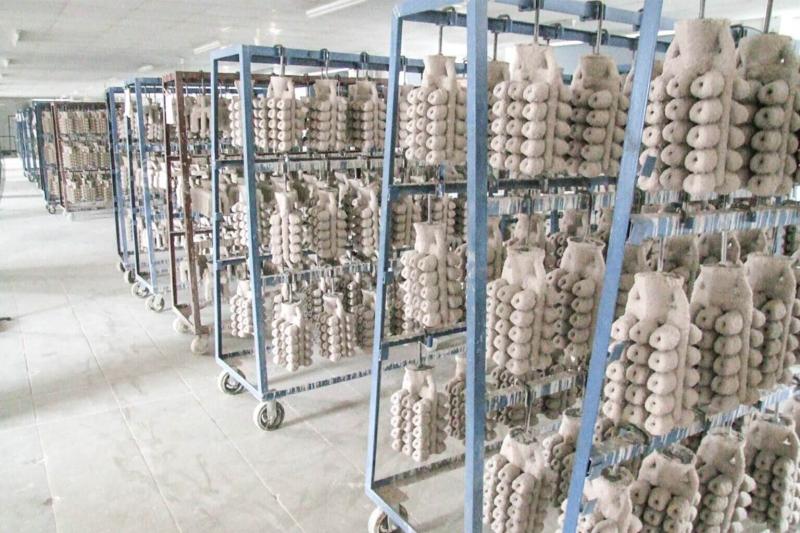
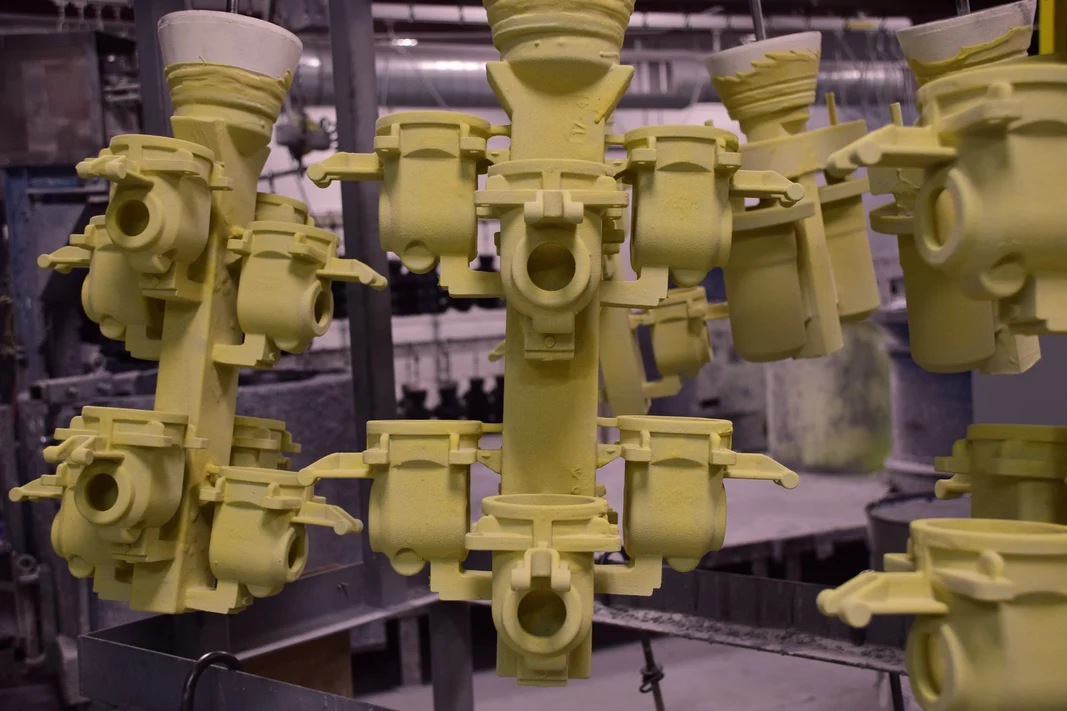
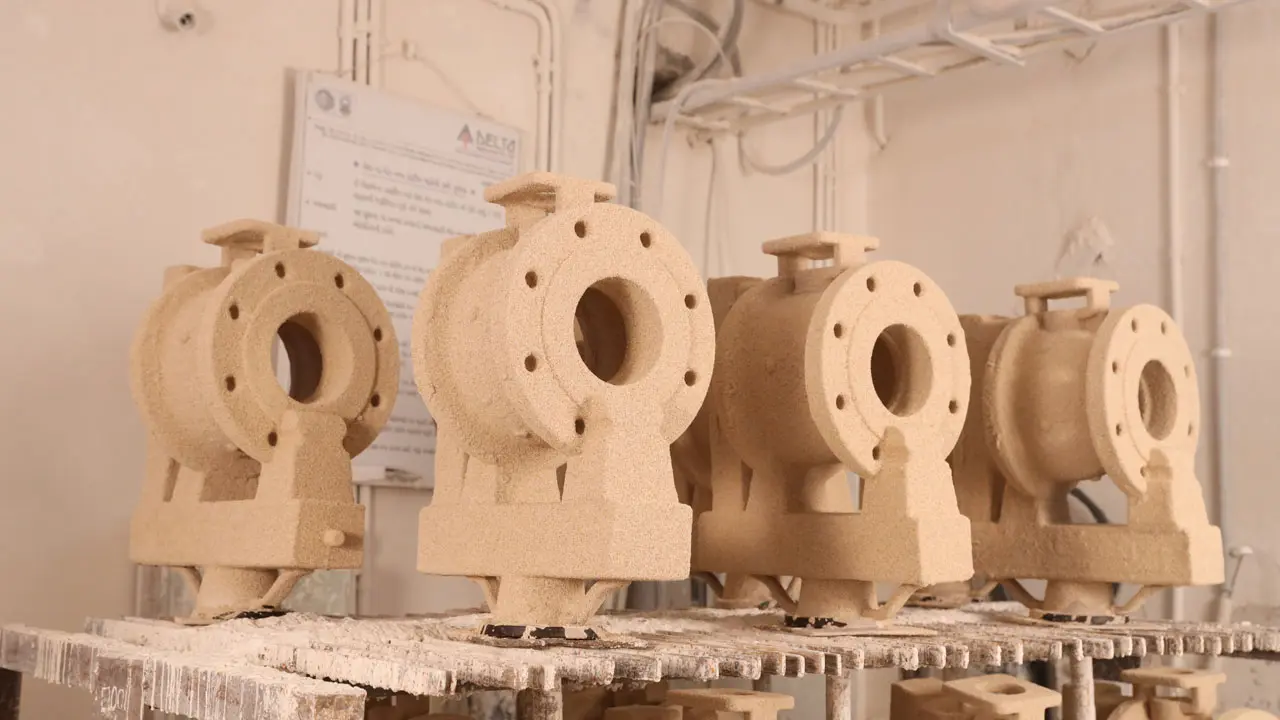
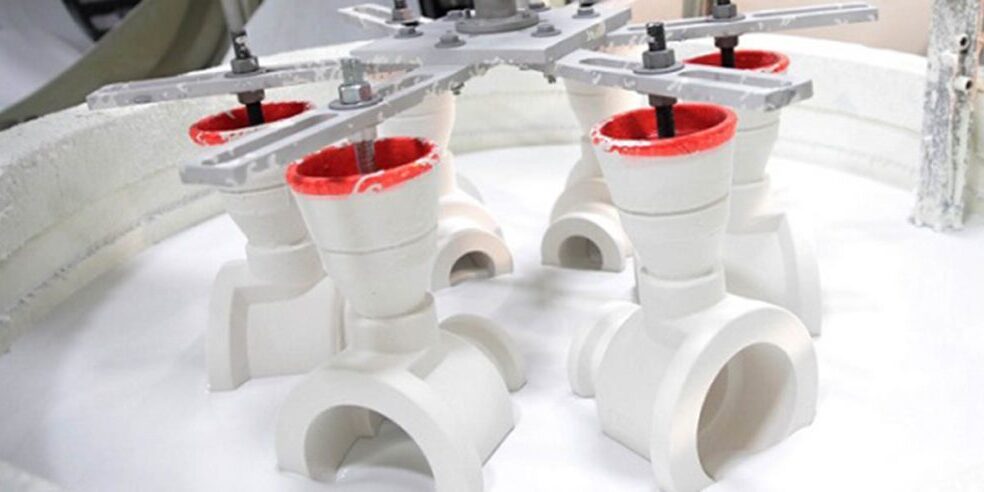
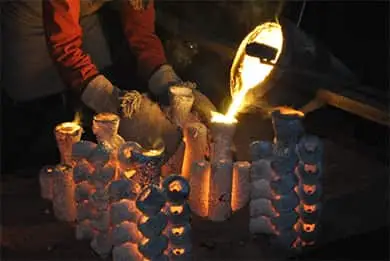